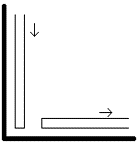
Starting Side doesn't touch Finish Side
Spacer Prestart Offset parameter may too low; increase.
Spacer Registration Parameters may be out of adjustment. Disable and adjust accordingly.
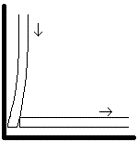
Starting Side pushes Finish Side over.
Spacer Prestart Offset parameter may too low; increase.
Spacer Registration Parameters may be out of adjustment. Disable and adjust accordingly.
Finish Side doesn't come down to bottom edge of Starting Side spacer.
Spacer Off Offset parameter out of adjustment. Decrease offset to cut the spacer nearer to the corner which will extend final edge of spacer.
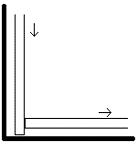
Finish Side goes down past bottom edge of Starting Side spacer.
Spacer Off Offset parameter out of adjustment. Increase offset to cut the spacer farther away from the corner to reduce final length of the spacer.
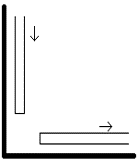
Starting Side starts too late and Finish Side doesn't go to bottom edge of Starting Spacer.
All 3 other corners rounded.
Tiny Dancer tractor drive is unclamped. Flip pneumatic thumb switch.
Tiny Dancer Spring Wheel has no slack. Release Tiny Dancer Tractor Drive and pull more spacer into head assembly. (Close tractor drive when finished.)
Conversion constant is too low. Increase and / or perform a length test. Big Dancer not providing enough spacer, check unwind reel assembly.
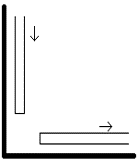
Starting Side starts too late and Finish Side doesn't go to bottom edge of Starting Spacer.
All 3 other corners are not rounded.
There may be a compound problem; see below:
- Starting Side doesn't touch Finish Side
- Finish Side doesn't come down to bottom edge of Starting Side spacer.
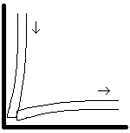
Starting Side pushes over Finish Side and Finish Side is too long.
All 3 other corners protruding.
Conversion constant is too high. Reduce and / or perform a length test.
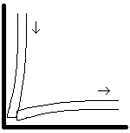
Starting Side pushes over Finish Side and Finish Side is too long.
All 3 other corners are not protruding.
There may be a compound problem; see below:
- Starting Side pushes Finish Side over.
- Finish Side goes down past bottom edge of Starting Side spacer.
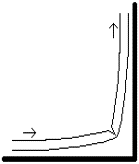
Both sides bow in and out of corner; the whole corner is rounded.
All 3 corners rounded.
Tiny Dancer tractor drive is unclamped. Flip pneumatic thumb switch.
Tiny Dancer Spring Wheel has no slack. Release Tiny Dancer Tractor Drive and pull more spacer into head assembly. (Close tractor drive when finished.)
Conversion constant is too low. Increase and / or perform a length test.
Big Dancer not providing enough spacer, check unwind reel assembly.
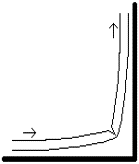
Both sides bow in and out of corner; the whole corner is rounded.
Only one or two corners:
There may be a compound problem; see below:
- First side is straight and then spacer bends out on second side.
- First side spacer is pulled away from corner, second side is straight.
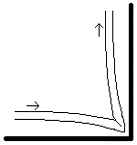
Both sides pull out towards the corner.
All 3 corners protruding.
Conversion constant is too high. Reduce and / or perform a length test.
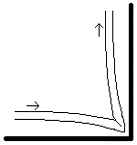
Both sides pull out towards the corner.
Only one or two corners:
There may be a compound problem; see below:
- First side is straight and then spacer bends out on second side.
- First side spacer is pulled away from corner, second side is straight.
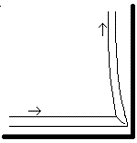
First side is straight and then spacer is pulled in on second side.
Knife offset is off. Increase knife offset to perform the corner cut earlier, farther from the corner.
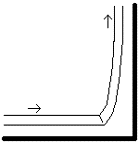
First side is straight and then spacer bends out on second side.
Knife offset is off. Decrease the knife offset to perform the corner cut later, closer to the corner.
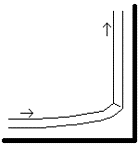
First side spacer is pulled away from corner, second side is straight.
Increase Backup Amount parameter
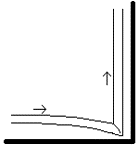
First side bends out toward corner, second side is straight.
Backup Amount parameter too high, decrease.
Bad Corners #1, #2 and / or #3 | |
---|---|
PROBLEM: | Spacer bends over in corner. |
SOLUTION: | 1. Spacer not sticking to glass well. See "Spacer does not stick to glass." |
2. Bad batch of spacer; check and replace as necessary. Wrinkled mylar on the roll is one of the indicators of a bad batch of spacer. | |
3. Glass isn't clean or dry. Make sure glass is both clean and dry. | |
4. Too much down-pressure from vertical guide wheel. Adjust pressure. | |
5. Not enough down-pressure from vertical guide wheel. Adjust spring tension. | |
PROBLEM: | Spacer pulls up in corner. |
See Spacer bends over in corner. | |
Edges | |
---|---|
PROBLEM: | Spacer is not properly located or misses glass completely. |
SOLUTION: | 1. Spacer offsets out of adjustment, check and adjust. |
2. Glass does not match network data. Correct if necessary | |
PROBLEM: | Spacer Does not stick to glass. |
SOLUTION: | 1. Glass isn't clean or dry. Make sure glass is both clean and dry. |
2. Bad or old batch of spacer. Replace wheel. | |
3. Too much down-pressure from vertical guide wheel. Adjust spring tension. | |
4. Not enough down-pressure from vertical guide wheel. Adjust spring tension. | |
5. Feed Conversion Constant incorrect. Not enough spacer dispensed per inch of travel. Run Test routine to set Feed Conversion Constant. | |
PROBLEM: | Spacer is not laying straight along side, bows and bends during straight-always. |
SOLUTION: | 1. This is often a sign that the spacer stuck poorly or not at all during the application process. See "Spacer does not stick to Glass." |
PROBLEM: | Starting spacer does not stick, bends away from center of glass. |
Ending spacer does not stick, bends away from center of glass. | |
Ending spacer does stick but is not straight. | |
SOLUTION: | 1. Spacer not sticking to glass well. See "Spacer does not stick to glass." |
2. Manually adjust spacer before placing top glass. | |
3. Make sure Prestart Spacer and Prestart Off Offsets are not set incorrectly, causing the starting and ending spacer to punch on each other or the guide wheels. | |
4. Spacer sticking or getting caught on guide assembly. Make sure entire head assembly is clean and free of debris, spacer and build up of sticky remains. | |
PROBLEM: | Spacer bunches up in feed or knife assembly while dispensing. |
SOLUTION: | 1. Spacer building up in knife area because too much spacer is being dispensed per inch or there is too much boost in corner. Check Feed Constant value through Test routine and reduce corner boost if necessary. |
2. Spacer building up in knife area because it is not fully feeding past the guide wheels as quickly as it is being dispensed by the feed wheel. Check for machine cleanliness. Reduce down-pressure on vertical guide wheel. | |
3. Knife dull; replace | |
Use extreme caution when adjusting knife assembly. Remove air when applicable. | |
Knife Cuts | |
---|---|
PROBLEM: | Spacer doesn't cut correctly. |
Corner cuts go all the way through | |
End cuts do not cut all the way through the spacer, leaving a notch rather than cut. | |
Cut or notch is at a marked angle. | |
SOLUTION: | 1. Spacer building up in knife area because too much spacer is being dispensed per inch or there is too much boost in corner. Check Feed Constant value through Test routine and reduce corner boost if necessary. |
2. Spacer building up in knife area because it is not fully feeding past the guide wheels as quickly as it is being dispensed by the feed wheel. Check for machine cleanliness. Reduce down-pressure on vertical guide wheel. | |
3. Knife dull; replace | |
Use extreme caution when adjusting knife assembly. Remove air when applicable. | |
PROBLEM: | Knife does not cut spacer does not cut all the way through to the bottom. |
SOLUTION: | 1. Knife dull; replace |
2. Knife out of adjustment. Make sure knife moves freely and square to cutting table. | |
3. Knife out of adjustment. Make sure knife is centered between rollers when extending. | |
Use extreme caution when adjusting knife assembly. Remove air when applicable. |